e sempre più eco
e sempre più eco
Esplora la gamma
Application Engineering e R&D Baltur guidano il futuro della tecnologia della combustione, progettando Bruciatori per applicazioni industriali e residenziali in grado di produrre bassissime emissioni NOx e CO, studiati sulle esigenze dei clienti e idonei per il funzionamento con combustibili alternativi.
Comfort residenziale e risparmio energetico grazie a Sistemi di riscaldamento efficaci e innovativi, Caldaie a condensazione di ultima generazione, certificate per l’idrogeno – murali, a basamento e da incasso – Moduli termici e Sistemi termici ad alta potenza.
Soluzioni intelligenti per la Climatizzazione con tecnologia Inverter Classe A+++/A++ con refrigerante a basso impatto ambientale, Ventilconvettori a parete, soffitto e pavimento con display integrato e Refrigeratori d’acqua reversibili.
Baltur punta sulle Energie Rinnovabili, proponendo una gamma di pompe di calore, accumuli inerziali, collettori solari, sistemi di distribuzione idraulica, controlli di sistema e sistemi ibridi Factory Made in differenti configurazioni per la personalizzazione di un comfort sostenibile.
Un mondo di servizi
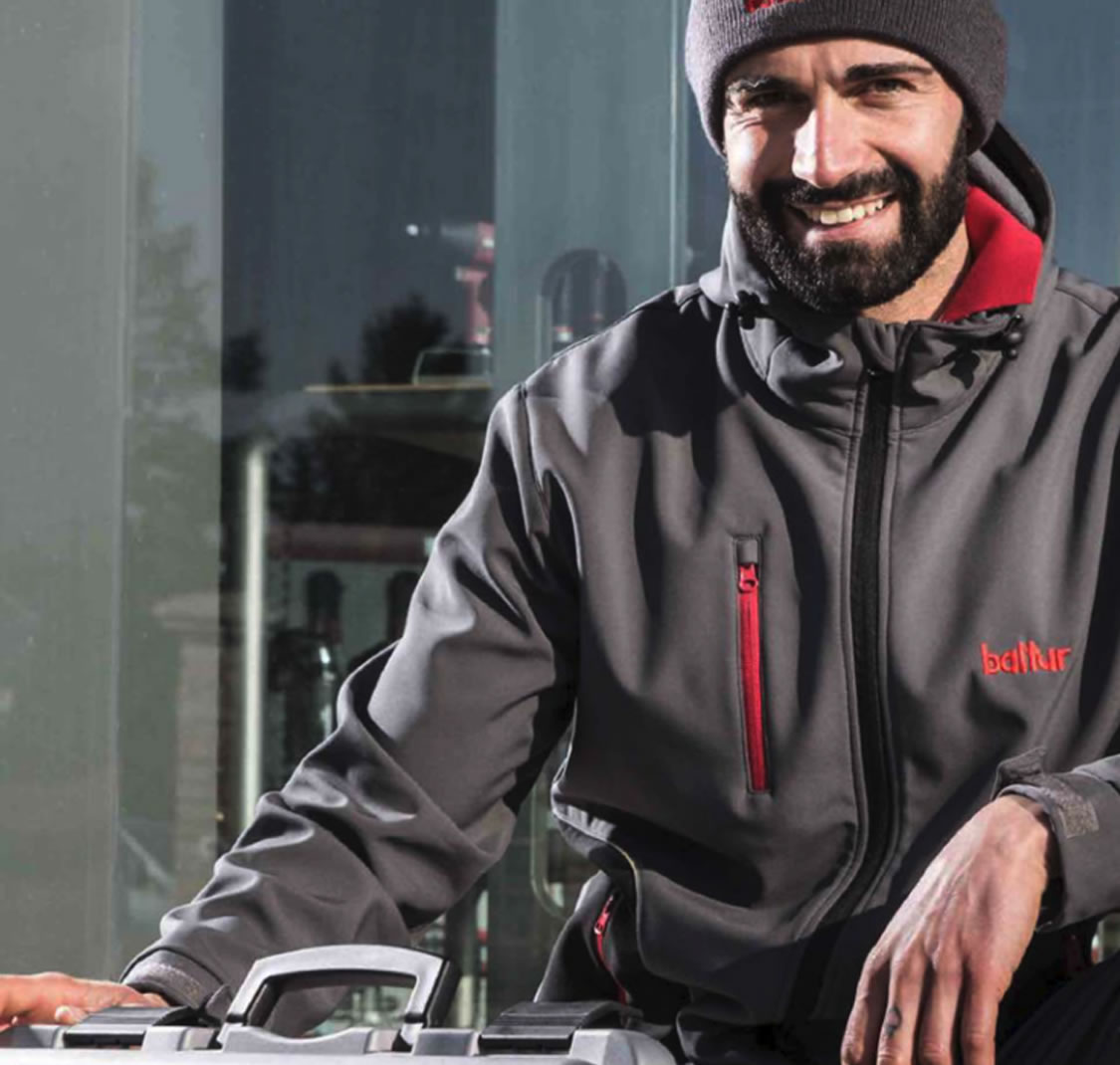
Pre vendita
Il Servizio di Pre Vendita è a disposizione della Rete Vendita e Installazione per analisi tecniche, studi di fattibilità, progettazione, valutazione economica, progetti speciali e fuori standard.
Vendita
Gli acquisti sono erogati attraverso la nostra Rete Vendita e Installazione in maniera capillare su tutto il territorio nazionale ed estero.
Post vendita
Il Post Vendita Baltur è a fianco della Rete Vendita in tutte le fasi dell’after sales, con flessibilità e disponibilità a sopralluoghi, collaudi e assistenza tecnica in sito e startup prodotti.
Formazione
La Formazione riveste un ruolo strategico e viene erogata in maniera continua, attraverso Baltur Academy, a tutta la Rete Vendita, Installazione e Assistenza.
Baltur, italiani da tre generazioni
Dal 1950, Baltur è un marchio d’eccellenza nelle tecnologie della combustione, con una gamma di prodotti che include caldaie, bruciatori a gas, e pompe di calore. In oltre 70 anni di attività, ha saputo raggiungere l’equilibrio perfetto tra performance e risparmio, comfort e sostenibilità, promuovendo sempre l’efficienza energetica e l’uso responsabile dell’energia.
Novità e approfondimenti
Rimani aggiornato sulle ultime tendenze e le innovazioni nel settore dell’energia e della climatizzazione. In questa sezione troverai approfondimenti su nuove tecnologie, normative e soluzioni sostenibili per un’efficienza energetica sempre maggiore. Che tu sia un professionista del settore o semplicemente un appassionato di tematiche ambientali, qui troverai contenuti utili e aggiornati.
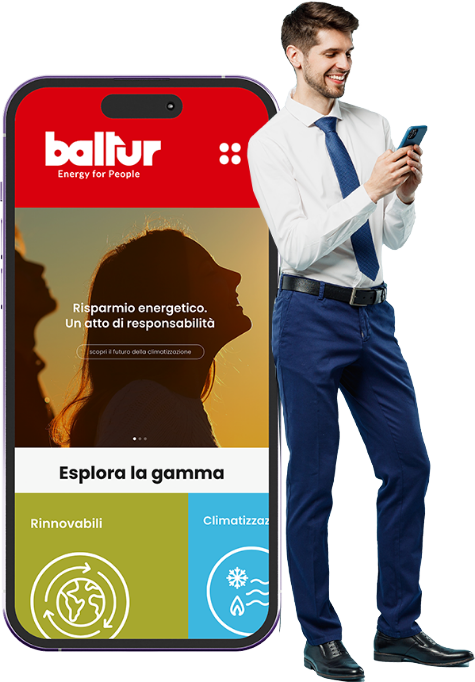